Enhancing Collaboration with a Digital Thread: PTC’s Creo’s Impact for Unified Product Development
How would you rate your company’s collaboration efficiency? Do you think your workflows are streamlined? Do you consider your product development processes smooth and successful? Many teams in various manufacturing industries struggle with fragmented tools and disconnected processes that hinder innovation leading to a long lead time for new product introduction (NPI). To overcome these challenges, manufacturers are turning to the power of the digital thread — a seamless flow and secure sharing of data that connects every stage of the product lifecycle.
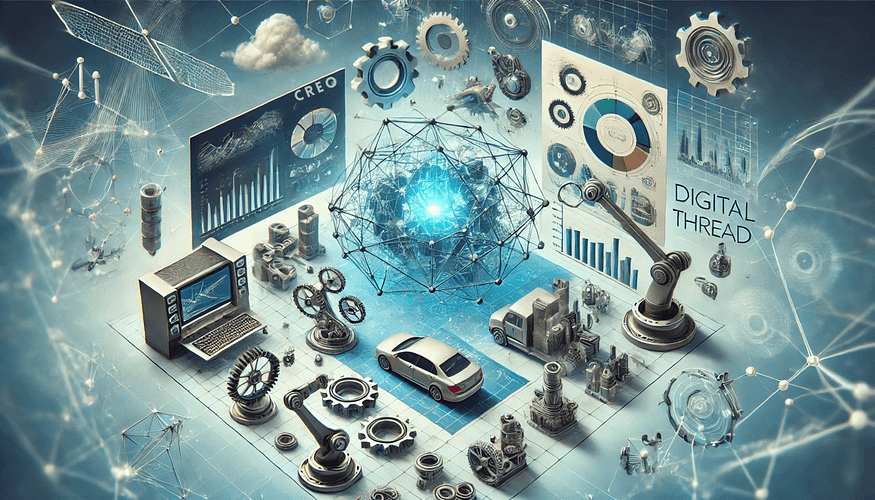
PTC Creo, a comprehensive suite of 3D CAD design and development tools, has capabilities to support the digital thread. By integrating all aspects of product development into one cohesive platform, Creo eliminates inefficiencies, improves collaboration, and drives innovation. In this article, we’ll explore common challenges in disconnected workflows and how Creo serves as the foundation for modern, efficient product development.
Key Takeaways
The Importance of the Digital Thread in the Product Lifecycle:
- A digital thread connects all stages of product development, ensuring seamless data flow, maximizing efficiencies, and reducing errors.
- Maintaining this thread allows teams to work collaboratively with up-to-date information, saving time and costs.
Challenges with Disconnected Workflows:
- Fragmented tools lead to miscommunication, manual updates, and redundant work, which slow down projects and introduce costly mistakes.
- A lack of integration results in disconnected processes and poor coordination between design, simulation, and manufacturing teams.
How Creo Solves These Challenges:
- All-in-One Platform: Creo integrates design, simulation, and manufacturing into a single system, eliminating the need for multiple software tools.
- Automatic Updates: Any design change propagates across all related files and processes, maintaining data consistency and reducing manual effort.
- Generative Design Tools: Engineers can explore multiple innovative ideas quickly, optimizing products for performance, weight, and manufacturability.
Real-World Benefits of Creo:
- Time Savings: Automatic updates across users prevent delays caused by manual rework.
- Early Validation: Integrated simulation tools help teams identify and fix problems before physical prototyping, saving money and resources.
- Streamlined Manufacturing: Manufacturing tools ensure designs are ready for production, reducing errors and shortening lead times.
Key Features of Creo:
- Multi-CAD Compatibility: Seamlessly work with files from other CAD systems like SolidWorks, SIEMENS NX, Inventor, AutoCAD, and CATIA using Unite Technology.
- Live Simulation: Real-time feedback on design changes helps engineers make informed decisions faster.
- Generative Design Tools: Optimize designs for optimal strength and weight, and/or for 3D printing with lattice structures and material-saving features.
Conclusion:
- Creo is a powerful tool for modern product development, empowering teams to innovate faster and stay competitive by maintaining the digital thread.
- Partnering with 3HTi ensures effective implementation and support, helping organizations maximize the benefits of Creo.
The Problem: Broken Connections in Product Development
Tools That Don’t Integrate or Work Well Together
Imagine a team designing an engine. One group uses a CAD tool to create the model, another uses a separate program for simulation, and the manufacturing team relies on yet another software for production planning. Each time the design moves to a new team, the data must be converted into a different format, risking the loss of critical details.
This lack of integration causes teams to spend unnecessary time recreating or fixing work, delaying the project. Every time information is passed along, the chances of errors increase.
Time-Consuming Processes
A single design change can trigger a chain reaction of updates. For example, if a part’s dimensions are altered it can affect other parts within the assembly and simulations may need to be run again. Manufacturing plans need to be updated, and product documentation must reflect the changes. If these updates are handled manually, the risk of mistakes grows.
Without an automated process, engineers and project managers waste valuable time coordinating these updates instead of focusing on innovation.
Communication Barriers
When tools and processes aren’t connected, communication across teams becomes a challenge. A supplier may unknowingly work with outdated files, or a remote team may not receive updates in time. These miscommunications can cause expensive mistakes leading to missed deadlines, and damaged relationships with customers or partners.
How Creo Solves These Problems
Creo addresses these challenges by serving as a single, integrated platform that connects the CAD, Pro-Engineer CAE and Pro-Engineer CAM stages of product development. This unified approach not only saves time but also ensures that teams stay aligned and focused.
All-in-One Solution
Creo offers tools for every step of product development — from sketching an idea to creating detailed designs, running simulations, and planning manufacturing. By consolidating all these capabilities into one system, Creo eliminates the need to switch between multiple software programs.
For instance, a 3D model created in Creo can be directly used for simulations (with multiple Creo Simulation tools), manufacturing, and creating assembly instructions without exporting any data out of Creo. This seamless integration reduces errors, ensures a smooth workflow and provides a better model for the manufacturing team.
Keeping the Digital Thread Intact
With Creo, all aspects of the development process remain connected. Any change made to a design automatically updates everywhere else ensuring consistency. If an engineer adjusts the size of a part, that change is instantly reflected in Simulation Services, manufacturing plans, and technical documentation.
This feature maintains the integrity of the digital thread, allowing teams to work with confidence and focus on innovation instead of chasing updates.
Generative Design for Smarter Solutions
Creo’s Generative Design extension take innovation to the next level. By setting goals such as minimizing weight or maximizing strength, engineers can explore multiple design options that meet these criteria. For example, a team designing a bike frame can use Creo to generate several potential configurations and select the one that best fits their needs.
Generative design speeds up decision-making, reduces material waste, and opens the door to creative solutions that might not have been considered otherwise.
Real-Life Examples of Creo in Action
Saving Time with Automatic Updates
Let’s look at an example of a Car door. Midway through the process, engineers realize the handle needs to be repositioned for better usability. In a traditional workflow, this change would require separate updates across simulations, manufacturing plans, and assembly instructions — a time-consuming and error-prone process.
With Creo, the change is automatically reflected everywhere. The simulation team can immediately validate the new design, manufacturing plans adjust in real-time, and documentation updates without manual effort. This saves time and ensures consistency.
Validating Designs Early
Creo offers advanced simulation tools that allow engineers to test their designs early in the process. For example, an aerospace company designing a wing component can use Creo’s simulation features to test how the wing handles stress and air pressure. If the design fails, engineers can make adjustments before moving to physical prototyping.
By catching potential issues early, companies save money on prototypes and avoid delays caused by late-stage changes.
Making Manufacturing Easier
Creo bridges the gap between design and manufacturing. Teams can use Creo to create machining plans, verify toolpaths, and ensure that designs are optimized for production. For instance, a team designing a metal bracket can seamlessly move from design to manufacturing without switching software. This integration reduces errors and shortens production timelines.
Exploring Creo’s Features
Multi-CAD Compatibility
In today’s global manufacturing environment, different teams often use different CAD Services. Creo’s Unite Technology makes it easy to collaborate by allowing users to open and edit files from other systems like SolidWorks, Creo vs. CATIA, Inventor, PTC Creo vs. Siemens NX CAD Software.
This capability eliminates the need for file conversions, ensuring that design intent is preserved and that teams can work together without technical barriers.
Live Simulation for Real-Time Feedback
Creo’s Live Simulation, powered by Ansys, provides instant feedback on a design’s performance. For example, if an engineer thickens a beam to increase strength, Live Simulation immediately shows how that change affects the structure’s ability to handle loads. This real-time feedback helps engineers make better decisions faster.
Additive Manufacturing Tools
Creo also supports 3D printing with its additive manufacturing tools. These tools allow engineers to optimize designs for 3D printing by adding lattice structures, reducing material use, and validating printability. This makes it easier to create lightweight, complex parts that traditional manufacturing methods can’t produce. This can be used based on the 3D printer you are using and is great for all materials including metals.
Conclusion
Efficient product development requires seamless collaboration, adaptability, and a strong foundation of connected tools. PTC Creo delivers on all these fronts by providing a single platform that maintains the digital thread throughout the entire process. With Creo, teams can save time, reduce costs, and focus on what matters most — creating high-quality, innovative products.
By eliminating inefficiencies caused by disconnected tools, Creo empowers manufacturers to innovate faster, meet tight deadlines, and stay ahead in a competitive market. If your organization is ready to enhance collaboration and optimize product development, 3HTi is here to help. As a trusted partner in implementing Creo and other PTC solutions, 3HTi offers tailored support, training, and expertise to ensure you get the most out of your investment. Contact 3HTi today to learn how Creo can transform your product development process and give your team a competitive edge.
Comments
Post a Comment